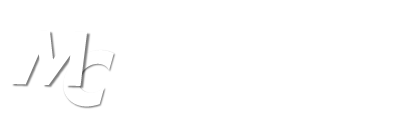
When designing chain drives, it is important to adhere to certain layout guidelines to assure optimum drive efficiency and life.
Chain selection and chain life will be adversely affected if these conditions cannot be met.
Determine the number of teeth of the small sprocket. The number of teeth for the large sprocket is determined by multiplying the number of teeth for the small sprocket by the speed ratio. More than 15 teeth on the small sprocket is recommended. The number of teeth on the large sprocket should be less than 120. Reducing the number of teeth on the small sprocket will reduce the number of teeth on the large sprocket.
Basic Formula for Selecting Drive Chain
Chain Wear Factors
Two important factors, resistance to wear and resistance to fatigue, should be considered when determining chain size and quality. Generally, these two factors dictate roller chain life and failure.
WEAR
Under normal circumstances, if a drive has been properly selected, the limiting factor for chain life is wear in the live-bearing area between the pin and bushing. Chain must be replaced when elongation, due to pin and/or bushing wear, prevents proper chain and sprocket contact. Appropriate attention to installation, lubrication and maintenance must be taken to assure maximum chain life.
FATIGUE
The stress variation caused by the maximum tension and slack on the chain during a complete drive cycle is fatigue. When chains are operated beyond their rate of capacity, fatigue becomes a dynamic part of chain failure. Chains will eventually fail from fatigue if subjected to high enough loads. The frequency and magnitude of the overload determine the amount of time the drive can operate before fatigue failure occurs. Satisfactory results in terms of hours or years of service can be obtained with proper roller chain and sprocket selection.